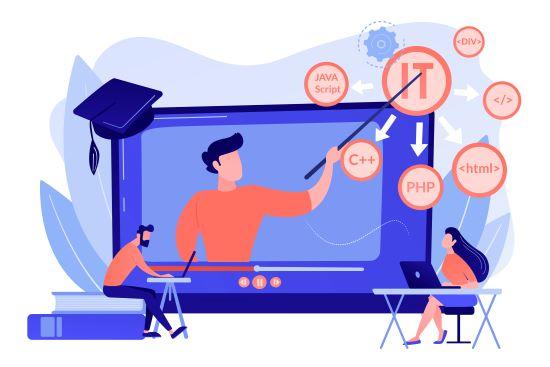
While visual inspection plays a key role in maintaining high-quality standards, it also has to overcome the challenges relating to the need for high-volume low parts to low-volume higher variants to align with customer-specific production needs
In today’s digital era, new-age manufacturing is resting on the advanced technology landscape that is constantly evolving. Simultaneously, the framework of visual inspection in manufacturing has overstepped the traditional OK and not OK (NOK) criteria for components to be inspected. Today, the simple black-and-white decision is a thing of the past and is replaced by a nuanced subjective approach based on human expertise and experience.
The QA personnel assessing the quality must be able to add variants or change thresholds of OK/NG for existing parts.
Here, introducing self-training software is a game changer, where users can independently train and deploy AI-driven models on the go. This phenomenon will soon become imperative today, where visual quality in manufacturing demands adaptability to reduce false positives and enhance overall efficiencies. This technology will enable manufacturers to achieve quality inspection independence and ensure their teams perform quality control of their ever-changing production lines quickly and efficiently. The self-training software leverages advanced AI technologies while continuously learning from diverse datasets and adapting to the variants. This activity can elevate the precision and efficiency of visual inspection to unprecedented heights.
Let’s look closer at the use cases for the self-training solution for visual inspection.
Staying ahead of the curve in the dynamic PCB Manufacturing
We all know the Printed Circuit Board (PCB) industry evolves more rapidly than sectors such as the automotive. New designs, components, and functionalities keep changing every six months in the PCB domain. In such cases, quality inspection becomes a constantly shifting target. Here, the traditional solutions that depend on pre-programmed algorithms fail to adapt quickly to frequent changes. Then, manufacturers must rely on self-training software where these models can effortlessly adjust to the ever-changing PCB designs and new requirements without human intervention. This is possible as the model learns from the previous inspection process and updates its knowledge base continuously by identifying new patterns and placing components appropriately, in addition to recognizing potential defects in the components. This new software also ensures that the visual inspection occurs smoothly and effectively.
Recognizing the diversity of the logistics industry
In the logistics sector, no two packages or cartons look alike, and shipments are diverse, making it challenging for visual inspection. Where traditional automated inspection systems could be more effective, self-training visual inspection software thrives in such cases. Manufacturers can train the software to recognize patterns across various carton sizes and shapes. These self-training models continuously learn about the unique features of every carton they come across and become capable of identifying any anomaly, fault, or irregularity with high precision. Streamlining the process, reducing defects, and establishing the safe handling of various carton boxes is possible with the self-training model.
Active sorting and grading in the food sector
Food products are presented in different shapes and sizes and change with market demand and the seasons. It becomes a challenge for traditional software to sort and grade them with constantly evolving standards. On the other hand, self-training software models for visual inspection can continuously alter their criteria for sorting and grading based on real-time data and the feedback received. Hence, food products that meet the latest quality standards are picked. Such flexibility benefits food manufacturers as it helps minimize waste with effective sorting and grading while ensuring they meet consumer demands and market trends.
Redefining thresholds in manufacturing – elimination of rigid thresholds
The traditional quality inspection models more often follow rigid thresholds where any defect that exceeds a specific size is flagged as Not OK. However, by leveraging self-training models, the quality control process is transformed by introducing flexibility, and any deviation exceeding the new accepted level is alerted. This adaptability has further empowered manufacturers by refining the approach to visual inspection, reducing the chances of false positives, and optimizing the production processes. This can be further enhanced by integrating with Business rules engines (BRMS).
Self-training will not replace the need for a data scientist but will assist in process drifts, annotating presence/absence, and the ability to change thresholds. It solves a subset of the problem; software significantly reduces the implementation time required to take cutting-edge AI deployment live in production environments. Moreover, the user interface can direct users with no machine vision expertise by training on new defects and new products to AI, making the process very intuitive. This software enables manufacturers to stay ahead of the curve. Self-training software is not just a tool but a critical asset that empowers organizations to thrive in the ever-changing landscape, maintaining efficiency, accuracy, and productivity.
Add new comment