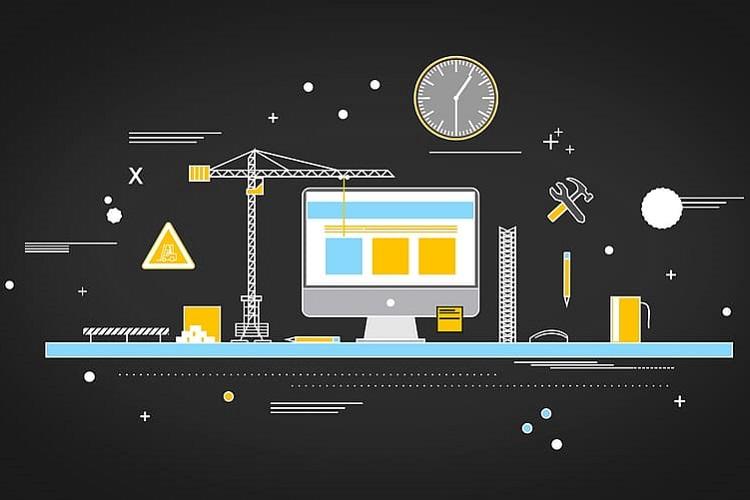
With the high level of uncertainty in manufacturing, supply chains and demand, that has been prevailing across the world in recent months, and economic growth coming to a standstill, it is pertinent that companies look at every potential opportunity of reducing costs and increasing margins. Most well-established corporations have likely already invested in efforts to optimize and streamline their plants, supply chain or procurement to an extent. So where is the opportunity to reduce costs even further? The one asset that manufacturing companies have not yet fully leveraged is Data. In today’s world, manufacturing organizations generate enormous amount of data and most have yet to recognize its vast potential.
Advanced analytics have enabled industries to have visibility to problems that they did not know existed in their processes. Problems related to product manufacturing, faulty suppliers, unused inventory in warehouses and several other bottlenecks can be easily identified and resolved with Data and Analytics. When added up, some of the seemingly small issues can result in considerable savings for companies.
Here are a few ways data and analytics can impact the manufacturing industry and lead to considerable improvements in organizations.
1. Increasing Supplier Accountability and Improving Quality of Parts Supplied
When trying to improve processes and reduce costs, companies often forget about the supplier aspect of their manufacturing chain. Faulty parts supplied by external vendors can lead to quality issues in the final product and thus cause unnecessary warranty claims from the end customers. In many of these cases the fault cannot be attributed to the supplier part and hence the warranty cannot be retrieved from the supplier. With the help of Analytics tools, organizations can gain visibility to these processes and identify and eliminate faulty suppliers from the system. While a Production Part Approval Process (PPAP) is a valuable tool for establishing competence of component suppliers, a lot of companies lose visibility to track defects after a PPAP is approved. Analytics can play a major role here, by providing visibility to the data that can help to track supplier performance and take necessary remedial actions.
2. Improving Methods of Demand Forecasting and Finding Ways to Reduce Unsold Inventory
In the manufacturing industry, strong demand forecasting can be a differentiator between a successful company and one that has too much unsold inventory at hand. Most companies tend to do forecasting based on historic sales only and do not consider a lot of external factors that can impact demand. Organizations can leverage predictive analytics to build projections of purchasing trends based on many more variables than simply using past sale numbers. This can greatly help in minimizing production waste.
In large-scale manufacturing units, Analytics can also be leveraged to reduce Zero Demand Inventory. By comparing Zero Demand components with active in-demand components, similarities can be drawn between them and their bill of materials and help organizations identify material that can potentially be repurposed to active parts.
3. Optimizing the Pricing Process
In most cases, large manufacturing companies use a method to price their products that considers the costs incurred, historical prices and the profit margins they intend to derive. This has proved profitable for most organizations. So, where is the role of Analytics in this? Analytics can be used in a big way to create pricing models that consider several external factors and come up with a price that helps drive volume as well as increase revenues. Companies that consider Frozen Standard costs at the beginning of the year and price their products based on that alone are losing revenue by not considering the fluctuation of raw material costs. Analytics can help bridge that gap by creating dynamic pricing models. Modern pricing algorithms take into account several external factors that include pricing fluctuation of commodities, competitor pricing, demand, whether or not the product is an IP to the company and many other factors.
4. Preventive Maintenance
Who wouldn’t want to solve a problem before it gets big? For companies that deal with equipment with high failure rates and downtime, it is an absolute necessity to carry out preventive maintenance. Preventive maintenance is often carried out when cued from visual inspections and documented parameter thresholds. A lot of times, this process is not enough to prevent failures. In the world of Analytics, it is possible to have automated triggers and warnings issued before a part fails, based on data accumulated through sensors. Real-time sensor data is captured and analyzed for deviations, enabling the prediction of maintenance events and component life.
Computer Vision and Deep Learning can also be used to identify anomalies without removing the parts. Technologies like Virtual Reality (VR) and Augmented Reality (AR) help visualizing the inside of parts and point to problem areas without having to remove a screw. This can save a lot in labor costs by avoiding the full teardown of large components.
5. Enabling Changes in Processes by Providing Visibility to Data
There are many ways Data and Analytics can help in optimizing processes and reducing costs, but one of the most basic things that Data and Analytics provides is visibility to data that can help in better decision making. Without building complex Data Science models and advanced analytics techniques, sometimes the simple visibility to data can have far reaching financial and operational impacts on an organization’s decision making. It can help to uncover critical information through various methods of data delivery like reports, interactive dashboards, chatbots, alerts, etc. and provides insights that can make big impacts in operations. These are inexpensive ways of leveraging data to make informed decisions.
So, what needs to be done to be able to start leveraging data?
To achieve these, companies need to have an Analytics strategy. This is the most important part. Companies are often happy with the status quo and thus don’t have a proper data strategy and roadmap defining where they want to go. An endorsement is needed from the leadership and a top down approach must be taken to have a successful Digital Transformation.
The other aspect of becoming a successful data-driven organization is to have a gradual, step-by-step process. Small investments with tangible results will help in developing more interests among the leadership and eventually lead to an increase in investments. Agile Methodologies help in a big way to achieve this by means of rapid prototyping and experimentation and then putting these experiments to use. Successfully operationalizing the small experiments and theories developed builds appetite for more. This is how relatively traditional companies forge their futures as data-driven organizations.
The author is Senior Product Manager, Data and Analytics at GE Transportation, a Wabtec company and NEXT100 Winner 2019
Add new comment