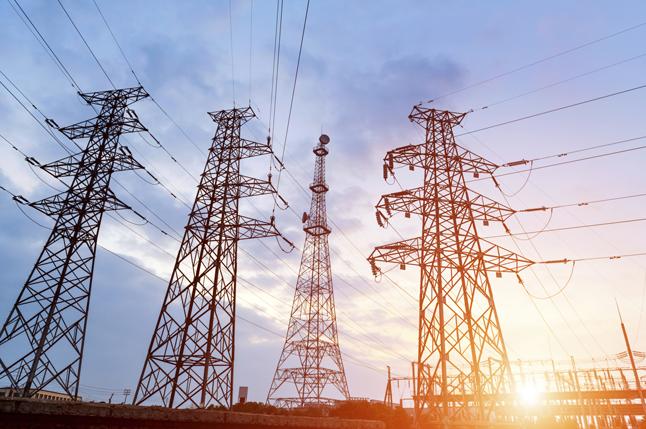
Power and utilities companies are reinventing their business environment with M2M technology in the face of constant pressure to improve profitability and reduce downtime. Sun Electric, a part of Sun Group of Companies, involved in electricity distribution business, has recently implemented a machine to machine technology to easily identify faults in the electric lines – and improve uptime for customers and profitability for the company.
Founded in 1989, the Sun Group of Companies specialises in sourcing and supplying electrical T&D equipment and allied material for utilities and turnkey contractors, involved in generation, transmission and distribution of electrical power. The company had a major problem of detecting the fault in the electric line. It used to take more time than fixing the problem itself. They wanted to do away with the trial and error method. Thus, they deployed a machine to machine platform from WebNMS.
The business problem
Whenever there is a fault in a network, the circuit breaker trips, disconnecting power supply of the entire network. And the network can be restored only if it has been cleared from faults. Detecting a fault is time consuming and it results in a power shut down for a long duration. Usually, the electrical maintenance team does it by trial and error method, which takes a lot of time.
On the other side, if the electricity department doesn’t supply power for an hour, not only the customer remains deprived of electricity but also the department loses revenue for an hour. “A network, which is up for maximum time increases revenue for the distribution company and also increases customer satisfaction,” says Dilip Closepet, VP Business Development, Sun Electric.
“We tried fixing this with a product called Fault Passage Indicators (FPI), but that stand-alone FPI was limited to the location where the fault was. This means the maintenance team had to patrol along the lines and identify the fault location. It was still expensive to patrol and identify the fault indicators – considering the location of network in remote sites, additional manpower and logistics. This made us look for an M2M solution that could ommunicate the fault information to any remote location. A scalable, customisable, and robust M2M solution was required for Sun Electric," says Dilip. They decided to evaluate WebNMS PowerGrid monitoring solution.
The technology problem
The major challenge they faced was communication. There are two channels of communication, one is communication from the sensor to the Remote Terminal Unit (RTU), and the other is RTU to control centre. This is where the M2M solution helped.
The distance (for communication) between the RTU and the sensor is short –, spanning about 5 or 10 metres, depending on where the RTU is placed on the electrical board. But from the RTU to the control centre, which they are doing over GSM, is where they faced issue in terms of presetting data to control centre, informs Dilip.
The M2M solution deployed
The solution consists of a hardware component (RTU) and software (WebNMS M2M platform) that provides remote fault indication with bi-directional communication. RTU communicates the fault information/ alerts to a central location or concerned maintenance personnel over GSM/GPRS. FPI is installed on the power lines, and the RTU is installed on the poles near the FPIs.
FPIs communicate with the RTU over radio frequency signals and RTU in-turn communicates with the M2M platform via GSM. The PowerGrid monitoring solution communicates with a central server, sending the information of the faults, and other data like fault logs, network current, settings of the FPI itself, health of the FPI, battery status of the FPI etc. The customisable energy dashboard also features the map of the city/country wherein the FPIs are installed, showing the precise locations and fault alerts. This helps in tracking faulty networks.
“We have deployed sensors at every electrical branching. We have deployed one RTU for every three sensors. All these devices communicate to a single M2M platform,” explains Dilip.
The benefits – uptime and productivity
A study done in Bengaluru, with 104 FPIs installed, has shown that the downtime has been reduced by nearly 43% after installing the FPIs as stand-alone devices, says a Sun Electric’s spokesperson. Considering the reduced downtime and reduced HR, there has been a saving of Rs 5.44 lakhs per year against an initial investment of Rs 13.00 lakhs. This means that the payback period is less than three years.
With the communicable FPIs with M2M solution, the outages due to faults will be reduced by 75%, and there will be a saving of Rs 9.48 lakhs per year against an investment of Rs 48.00 lakhs, with a highly increased customer satisfaction and reduced expenses on vehicle infrastructure, which are not quantifiable, says the company spokesperson.
Elaborating on why they had chosen WebNMS solution, Dilip says, “The degree of customisation that we could do with WebNMS was really amazing.” He further states, “Our users are not highly qualified to use computers and hence WebNMs got the solution simple enough so that everyone can use it.”
What's up next?
The company is collecting feedback from customers to go to the next level. "We’re planning to deploy the solution in cities ofOman andHo Chi Minh City inVietnam in the coming days,” informs Dilip.
Add new comment